Globalization has brought the world and human life vulnerable to strong competition.
According to Carpinetti, Buosi and Gerolamo (2003) this phenomenon has been leading to the emergence of new scenarios in which the industry must continue to apply the practice of principles best management, strategy and technology to stay competitive in the global world.
Bedi (2008) also stated that quality management has become increasingly significant and very important in management of an organization whether based on products or services in addition giving more focus to the quality management process.
Thus, a successful organization will not be making quality management a patchwork of management innovation, on the contrary making quality management a new method in developing products and services (Goetsch & Davis, 2013).
Efforts to improve quality and the need to improve quality in services have become increasingly common in all areas of society.
Sany Sanuri et al., (2011) stated that a clear understanding of concepts and systems quality management relies heavily on clarity on what quality means.
Generally, quality is quite difficult to produce if the organization does not implement quality management system effectively.
Through the implementation of an effective quality management system, it will create a strong quality culture in the organization which is fundamental to the implementation of quality management principles in an organization.
Continuous improvement is a shared quality management principle in developing and implementing a strong quality culture in the organization.
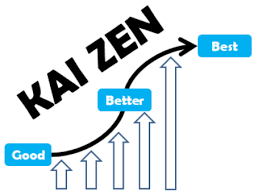
Continuous improvement effort should be seen as an organizational management strategy with the objective of improving work processes aimed at providing a service better quality to customers.
In cultivating continuous improvement several things need to be emphasized. Among them is the development of infrastructure necessary to implement improvements on an annual basis, identify specific areas that need to be improved and implement improvement projects as each field requires different improvement projects.
Apart from that, it is necessary to create a project team responsible for implementing and completing each improvement project that has been identified as well as providing all the necessary facilities in preparation for any problems that arise by identifying the cause, formulating solutions and creating controls that will be able to maintain the success that has been achieved.
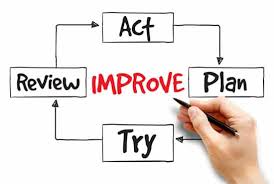
Continuous improvement efforts usually need to be integrated and incorporated into work processes and management, which will become a work culture.
This is important so that the quality aspect continues to be given the main emphasis in every process to ensure the production of quality products.
There are many studies that have been done show the results that there is a positive relationship between quality improvement strategies, management perception, customer engagement, information quality improvement to create a competitive consistency that benefits the organization towards achieving high quality status.